April 22, 2024
Refining is the final step in a long line of treatments that are used to extract copper and other metals from the raw ores that are mined in Bingham Canyon. The Kennecott refinery uses the electrolysis method of refining, a technique that has been around since about 1875. Between 1875 and 1891, most of the cooper refined by electrolysis came from Arizona. During this period, copper produced by electrolysis was substandard, the reason being that the electric generators of the time could not produce enough electricity to yield a quality product. After 1891, improvements enabled electric generators to provide a large and steady source of electric power, which in turn resulted in a better copper product (Navin 1978). The most significant improvement to the electric generating system was the switch from direct current to alternating current using a three-phase generating system instead of the single-phase and double-phase systems currently in use at that time. This system was first put on display as part of the 1891 International Electro-Technical Exposition in Frankfurt am Main, Germany (W nd.)
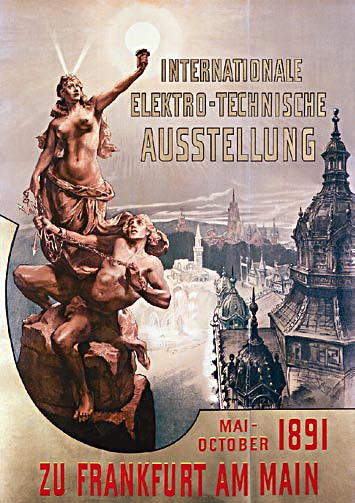
Official poster for the International Electro-Technical Exhibition 1891 (Wikipedia 2021).
Prior to the involvement of the Guggenheim family in the Bingham Canyon mines, the bulk of the ores shipped from Bingham Canyon were smelted at the Bingham Consolidated smelter in Midvale, Utah. Around 1904, with financial backing from the Guggenheims, Utah Copper Company (UCC, not yet Kennecott) began to expand its mining and milling operations. At the same time, the American Smelting and Refining Company (ASARCO)—in which the Guggenheims were majority owners—was buying up majority interests in existing Salt Lake Valley smelters with the goal of consolidating them into one large smelting operation at Garfield, Utah (Strack 2022). Work on the Garfield smelting operation plant began in 1905 and in 1907, ASARCO bought the Baltimore Electrolytic Refining Company (established 1891) in Baltimore, Maryland, making ASARCO and the Guggenheims major players in the copper processing industry (Navin 1978).
In a deal brokered by the Guggenheims, UCC was obligated to send all concentrate (ore with the gangue [unwanted material] removed) to ASARCO for smelting and refining. This arrangement was immensely profitable for the Guggenheims and mutually beneficial for both the UCC and ASARCO (Navin 1978; Salt Lake Mining Review [SLMR] 30 August 1906:28-29; Strack 2022). The arrangement, however, was not without its problems. Over time, an uneasy relationship developed between the two companies and during World War II, a dispute arose between Kennecott and ASARCO over smelting fees. The fees disagreement was settled in Kennecott’s favor, but Kennecott had an additional grievance, the condition of the smelter at Garfield (Navin 1978). Kennecott complained that the antiquated smelter (completed in 1906) was not operating at its full potential and needed repairs and improvements (Strack 2022). The repairs and improvements, however, cost more than ASARCO was willing to invest. In order to resolve their differences, an agreement was reached between the two companies which allowed each to gradually reduce their dependence on one another. The highlights of the agreement were that Kennecott would do the following: build its own smelter in Hayden, Arizona (completed in 1958); buy and renovate the Garfield smelter (completed in 1959); and build their own refinery in Baltimore, Maryland (completed in 1959) (Navin 1978).
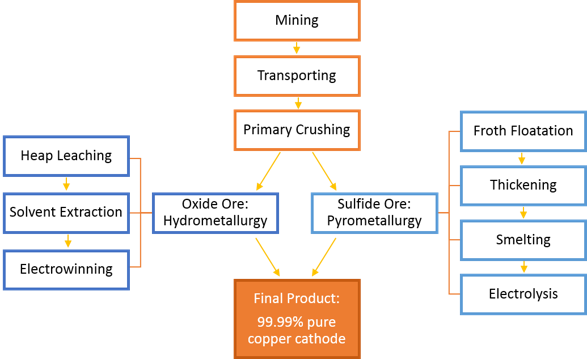
The process through which copper ores proceed, from excavation to refining (Superfund nd.).
In 1948, Kennecott began building its first refinery in Garfield, Utah, approximately 1.5 miles east of the Garfield smelter. It was finished in 1950 at a cost of $17 million (Hoffman 2005; Navin 1978). Refining at the new mill was a two-step process. The first step was electroplating, a 28-day process where 760-pound copper anodes (99.6% cooper) were placed in concrete cells (or tanks) containing an electrolyte solution and a pure copper starter sheet (cathode) was placed between the anodes. Low voltage passing through the cells would dissolve the anodes and the resulting copper particles would migrate to the cathode, resulting in a product that was 99.96 percent pure. During the second step the cathodes were removed from the electrolyte solution by overhead cranes and the cells were drained. The slimy residue was washed from the cells and anodes, with the slime sent for processing at the precious metals facility and the anode scraps returned to the smelter for recasting (Hoffman 2005).
The cathodes were washed, stacked, weighed, banded, and prepared for shipping. In the electrolyte purification section of the refinery, used electrolyte was purified by removing soluble impurities, such as arsenic, nickel, iron, and lead. Insoluble impurities, such as gold, silver, platinum, and selenium, found in the waste sludge, were sent to the silver refinery for extraction. In 1988, the refinery had the capacity to process 240,000 tons of cathode copper per year. Valuable by-products from the refining process included gold and silver, with annual averages of 295,000 ounces of gold and 2,250,000 ounces of silver (Hoffman 2005).
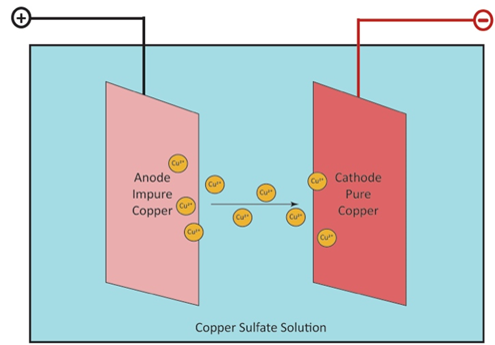
Electrolysis, the final refining process (Superfund nd.).
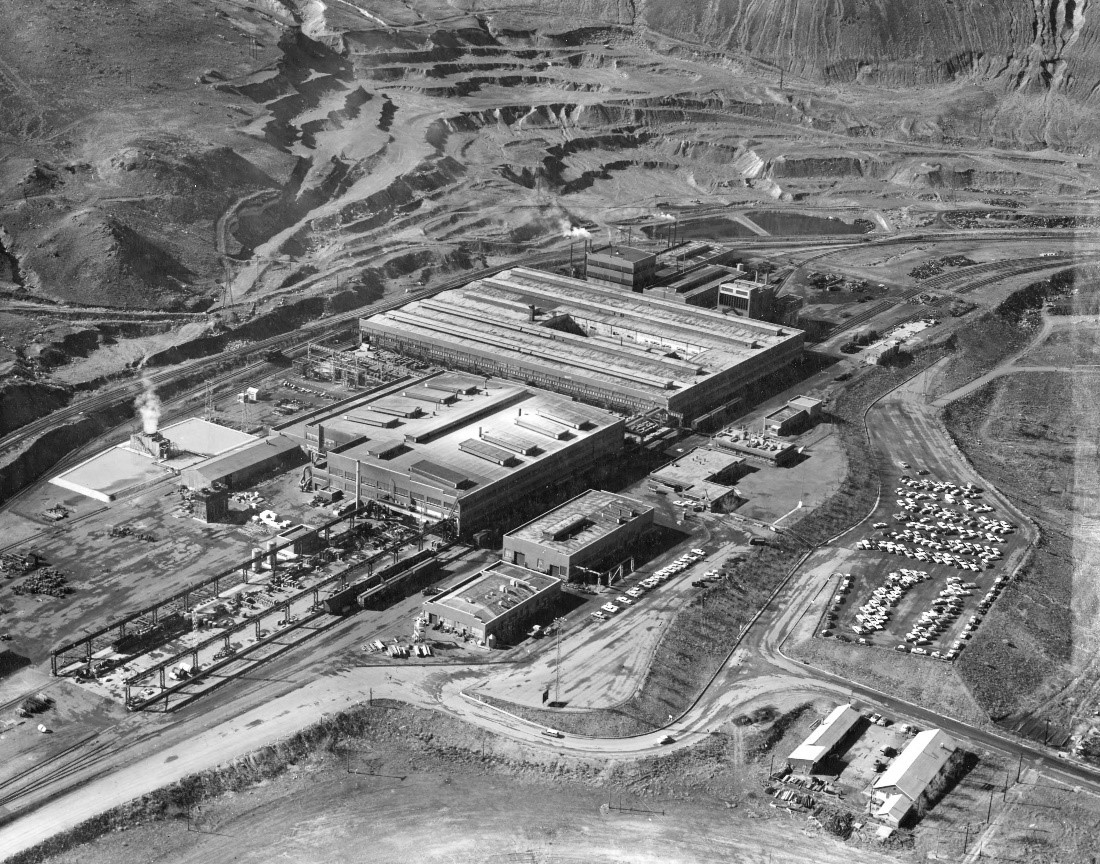
Kennecott refinery, 1962 (Rumel 1962).
In order to match the production rate of the new smelter (built 1995*), the refinery was updated in 1995 with the hopes of increasing capacity to 310,000 tons per year. Modernization included automation which would reduce costs by 35 percent, modifications to the existing tank house (the area in which anodes and cathodes are processed), and an upgrade to the electrorefining process (stainless steel starter sheets replaced the earlier copper sheets). In addition, a new precious metals building was erected that would use a new processing method. In total, these upgrades cost $164 million. At this time, the copper anodes from the smelter were 98.5% pure and when the refining was complete, the copper cathodes were 99.9% pure. The new precious metals plant produced gold in 5 days instead of the 45 days required in the past. The average output of the new precious metals plant was 500,000 ounces of gold and 4,000,000 ounces of silver per year (Hoffman 2005).
In 2010, Kennecott installed a $10 million, 6 mega-watt combined heat and power system that supplied more than half of the refinery’s electric power. The primary fuel required for operating the system is natural gas, thus greatly reducing the need for electricity provided by coal-powered grids. The system recycles waste heat into steam and reduces carbon dioxide emissions by 36,000 tons. Also, nitrogen oxide and sulfur dioxide emissions are greatly reduced. The system has an efficiency rating of 80 to 82 percent.
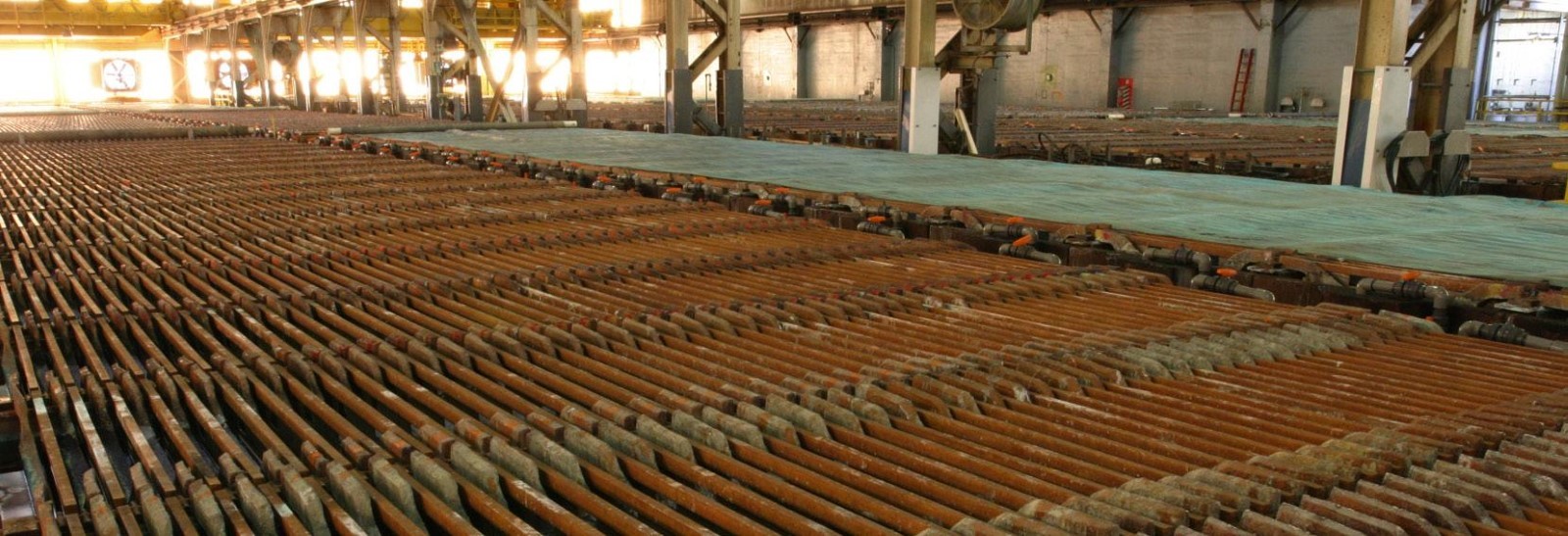
Anodes and cathodes suspended in solution inside the tank house (Project Profile 2015).
In 2015, Kennecott was the second largest producer of copper in the United States and supplied the United States with one quarter of its copper supply. On average, Kennecott produced 300,000 tons of copper cathodes. By-products of Kennecott ‘s copper production included an annual average of 500,000 ounces of gold, 4 million ounces of silver, 30 million pounds of molybdenum, and one million tons of sulfuric acid (Project Profile 2015).
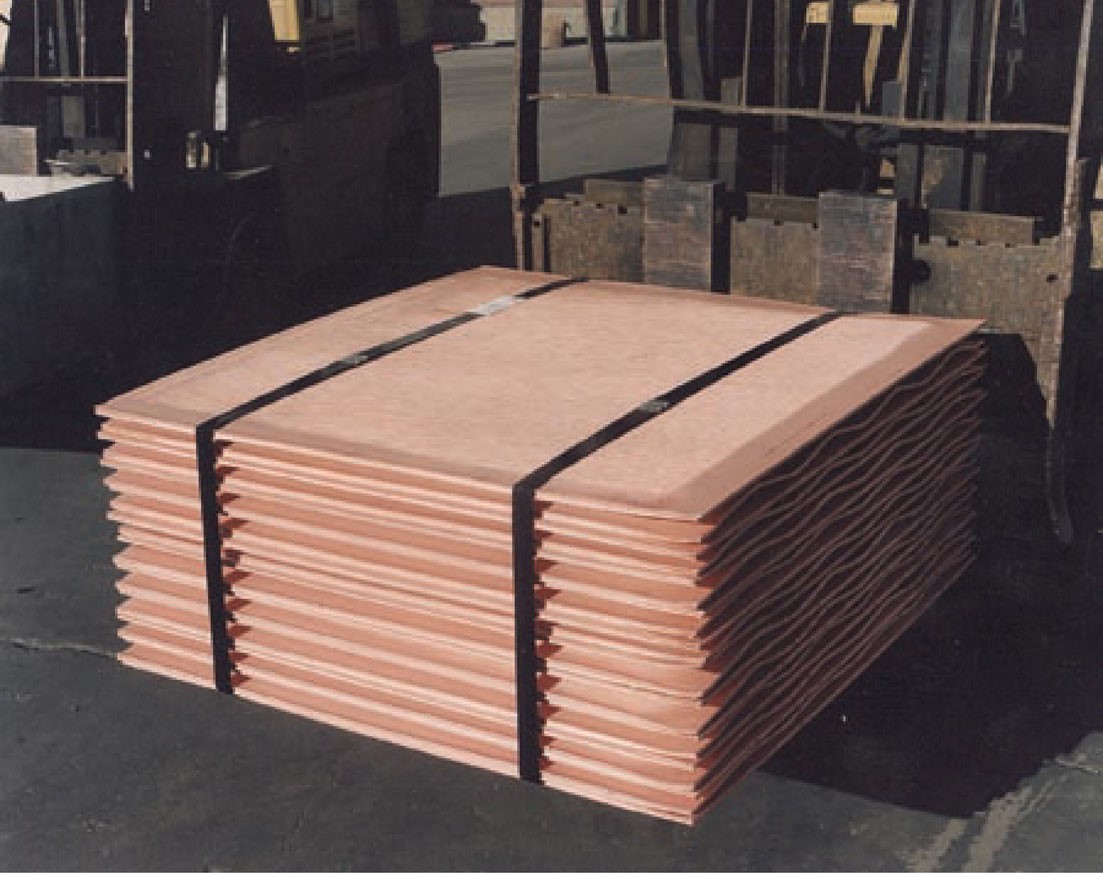
Finished cathodes, bundled and ready for shipment (Project Profile 2015).
*This was the third smelter built in this location, the first built in 1905 by ASARCO, the second built by Kennecott in 1978.
Credits
Grant Fahrni, Logan Simpson